A qualificação e a certificação dos operadores de altos-fornos
Redação
O alto-forno é um reator que utiliza o princípio de contracorrente, onde os gases em ascensão reagem e transferem calor para sólidos e líquidos descendentes. Ou seja, é um processo destinado à produção do ferro-gusa, a partir da reação química de redução de óxidos de ferro. O ar pré-aquecido é soprado pelas ventaneiras e entra inicialmente em contato com o carvão vegetal na região denominada raceway ou zona de combustão. O contato do oxigênio do ar soprado com o carbono do carvão vegetal, pré-aquecido na faixa de 1.400°C, provoca inicialmente a reação de produção do dióxido de carbono. Esta reação altamente exotérmica, produz grande quantidade de calor para o processo. Contudo, o dióxido de carbono formado, nesta região de alta temperatura, reage imediatamente com mais carbono do carvão vegetal para formar o monóxido de carbono, reação esta conhecida com de solution loss ou boudouar. Por sua vez, a umidade contida no ar soprado entrará em reação com o carbono do carvão vegetal, gerando os gases redutores CO e H2. Embora estas reações sejam endotérmicas, ocorrendo portanto absorção de calor, o resultado efetivo associado à saída de gases redutores do raceway é o aporte de grandes quantidades de calor fornecido para a sequência do processo, gerando uma temperatura de chama na região que excede 1.850°C. Durante o restante do seu caminho pelo alto-forno, o gás ascendente suprirá calor para as camadas de carga metálica descendentes, saindo no topo do forno ainda com temperaturas acima de 100°C. Na medida que os gases (CO e H2, além de N2 de sopro) saem do raceway, eles ascendem no forno entrando na região de gotejamento da carga metálica. Dentro desta região, o metal líquido e a escória percolam através do leito de carvão vegetal em oposição ao movimento ascendente dos gases. É ainda dentro desta região que o metal atinge o seu teor final de silício, sendo que quanto maiores forem às quantidades de calor disponível e altura de percolação, maior será a transferência de silício para o ferro gusa. As exigências de qualidade do ferro gusa, para sua posterior utilização, geralmente requerem baixos teores de silício, mas, existem limites associados à segurança operacional de um alto-forno, que impedem a queda de temperatura nesta região para o controle do teor de silício final do ferro gusa. Deve-se entender os requisitos e a sistemática para a qualificação e certificação de operadores de altos-fornos a carvão vegetal e coque metalúrgico.
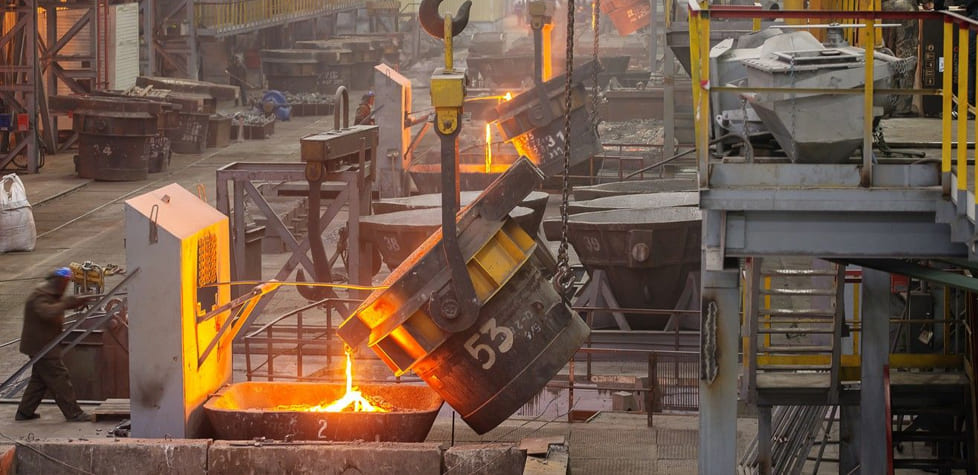
Da Redação –
A fabricação do aço ocorre geralmente na obtenção do chamado ferro gusa, material metálico composto majoritariamente por ferro, porém contendo também altos teores de carbono, da ordem de 4,5%, e altos teores de impurezas (enxofre, fósforo e outros elementos). Isso é produzido a partir do minério de ferro aglomerado sob a forma de sínter ou pelotas, obtidos respectivamente nos processos de sinterização e pelotização, ao qual são adicionados fundentes (cal, sílica e substâncias semelhantes) e o chamado coque metalúrgico (basicamente o resultado da coqueificação do carvão mineral ou vegetal).
Depois disso, sucede-se a conversão do ferro gusa em aço na chamada aciaria, onde nos conversores ocorre basicamente a oxidação do excesso de carbono e das impurezas, que são assim removidos, resultando numa liga ferrosa com teor de carbono bem mais baixo, em geral inferior a 1%, e com baixíssimo nível de impurezas, que pode ser considerado residual. A obtenção de ferro gusa geralmente ocorre no chamado alto-forno, embora um material quimicamente semelhante, porém com aspecto esponjoso possa ser obtido pelo processo de re...